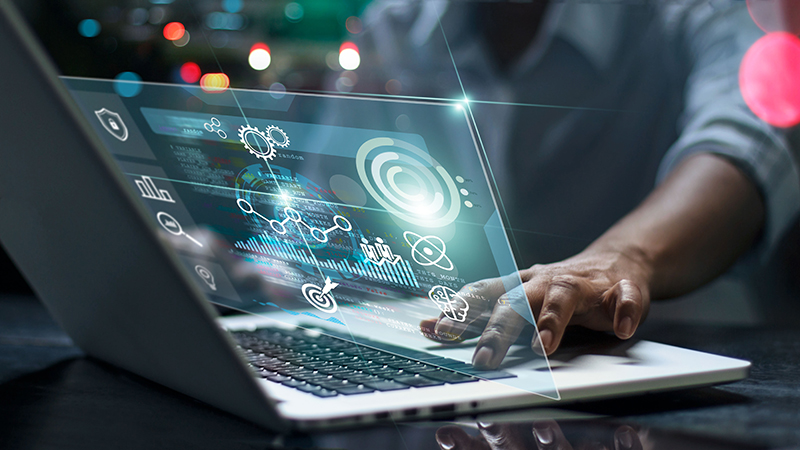
Advanced Process Control (APC) is thus essential today in the modern plant. Small differences in process parameters can have large effects on profitability; get it right and profits continue to grow; get it wrong and there are major losses. Many applications of APC have pay back times well below one year. APC does require a detailed knowledge of the plant to design a working system and continual follow up along the life of the plant to ensure it is working optimally. Considerable attention also needs to be given to the interface to the operators to ensure that they can apply these new technologies effectively as well.
By the end of this course delegates will be able to:
Electrical engineers, instrumentation and control engineers, process control engineers, process engineers, senior technicians, automation engineers, chemical engineers, chemical plant technologists, system integrators
This interactive Training will be highly interactive, with opportunities to advance your opinions and ideas and will include:
• Lectures
• Workshop & Work Presentation
• Case Studies and Practical Exercise
• Videos and General Discussions
Fundamentals of Process Control
Fundamentals of Tuning PID Loops
Internal Model Control (IMC)
Model Predictive Control (MPC)
MPC: Model Representations
MPC: Model Identification
MPC: Control
Reference Models
Control Formulation Problem
MPC Steady State Optimisation
A RECTUS attendance certificate will be awarded to all participants who complete at least 80% of the total course duration.
Code | Date | Venue | Fees | Register |
---|---|---|---|---|
IE100-04 | 12-10-2025 | Dubai | USD 5450 |
Providing services with a high quality that are satisfying the requirements
Appling the specifications and legalizations to ensure the quality of service.
Best utilization of resources for continually improving the business activities.
BTS keen to selects highly technical instructors based on professional field experience
Since BTS was established, it considered a training partner for world class oil & gas institution
1st floor, Incubator Building- Masdar City - Abu Dhabi - United Arab Emirates
Sun to Fri 09:00 AM to 06:00 PM
Contact Us anytime!
Request Info